Soft Magnetic Ferrite Dies | Ferrite Mold Manufacturer
Ferrite is the most widely used permanent magnet material. It is manufactured by powder metallurgy. It is mainly divided into two types: barium material (Ba) and strontium material (Sr), and is divided into two types: anisotropic and isotropic. It is a kind of permanent magnet material that is not easy to demagnetize and not easy to corrode. The maximum working temperature can reach 250℃. It is hard and brittle. It can be cut and processed by tools such as diamond sand, and it can be formed at one time with a mold that is just processed by alloy. Such products are widely used in permanent magnet motors (Motor) and speakers (Speaker) and other fields.
Ferrite Dies has reasonable structure, stable quality, high forming accuracy, and the use of cemented carbide wear-resistant materials in the mold cavity, which can better improve the service life of the mold. The heterosexual mold realizes the axial, radial, composite orientation and multi-pole orientation of ferrite and injection molded NdFeB..
In the past over 10 years, PTJ has been focusing on technical researching, production and marketing of Carbide dies. And provide the best Carbide dies and various electronic application solutions for cutomers from world wide. You always can find out a suitable Ferrite dies case studies for your product in our official website.
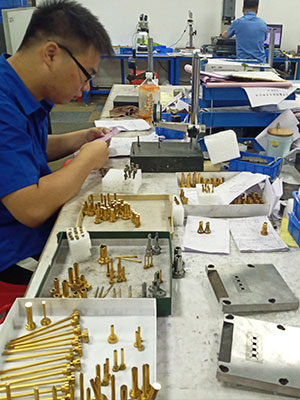
Standard Ferrite Mold by PTJ:
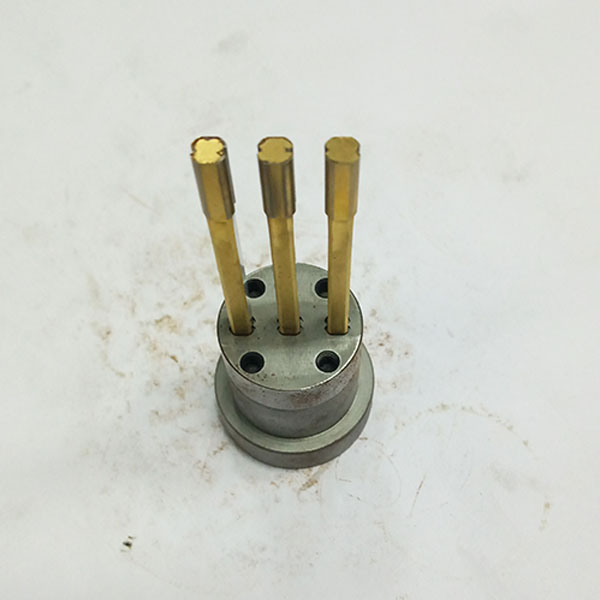
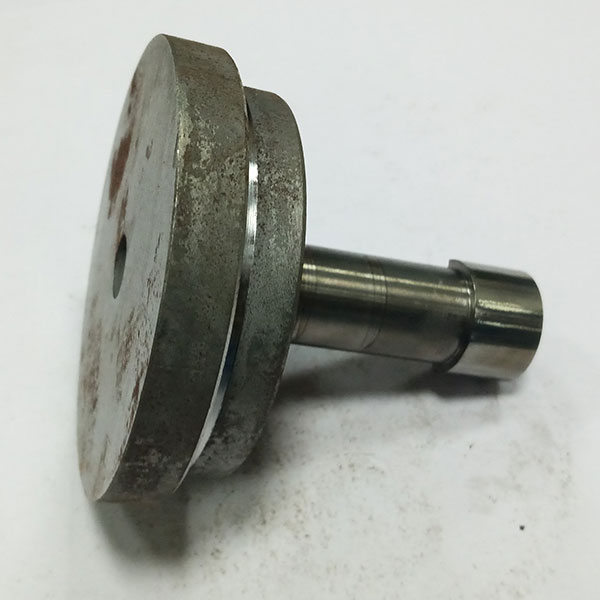
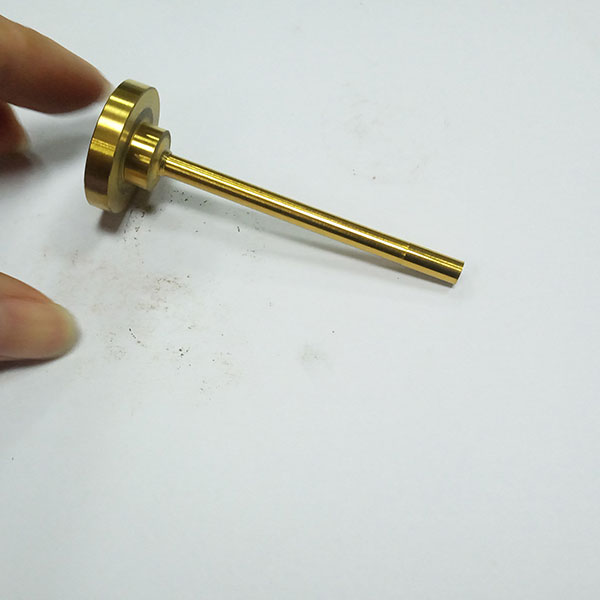
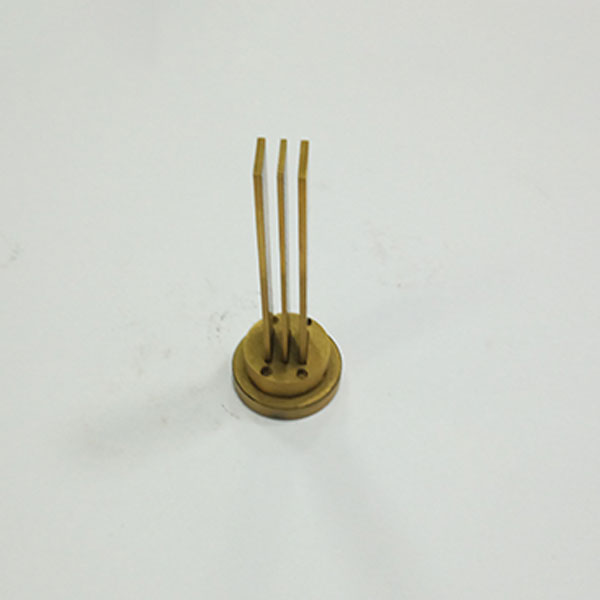
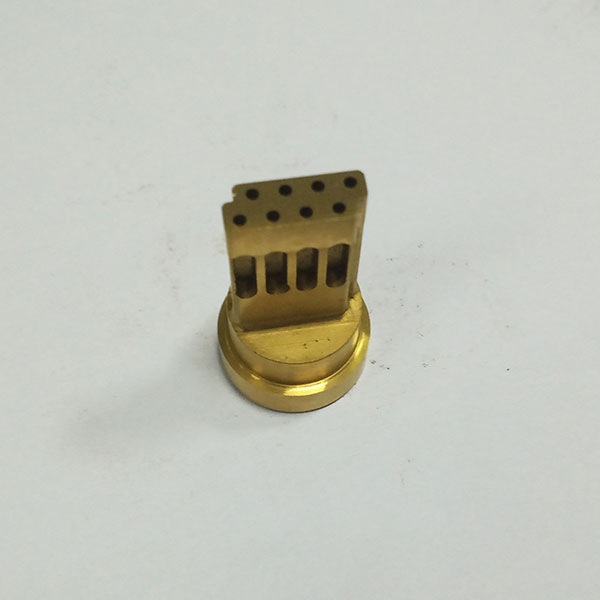
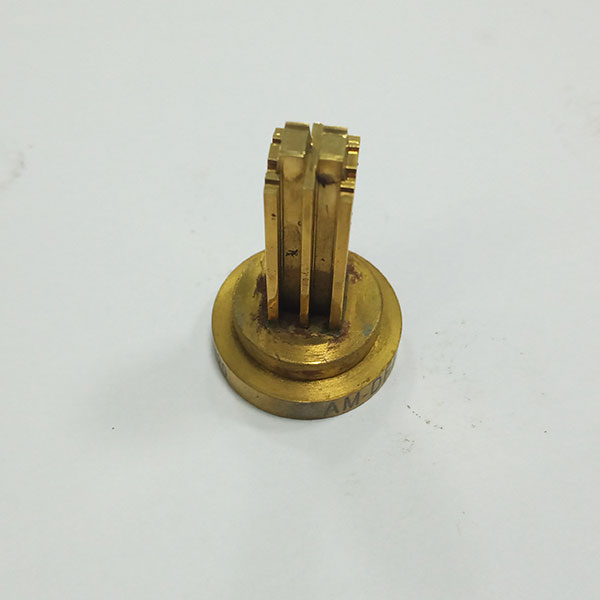
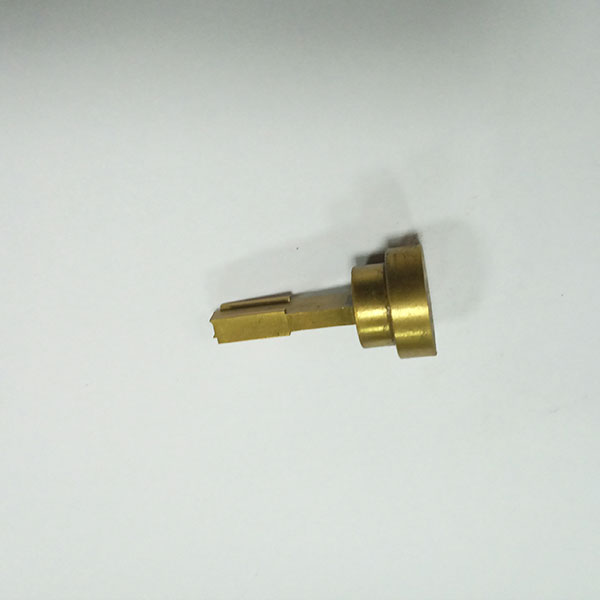
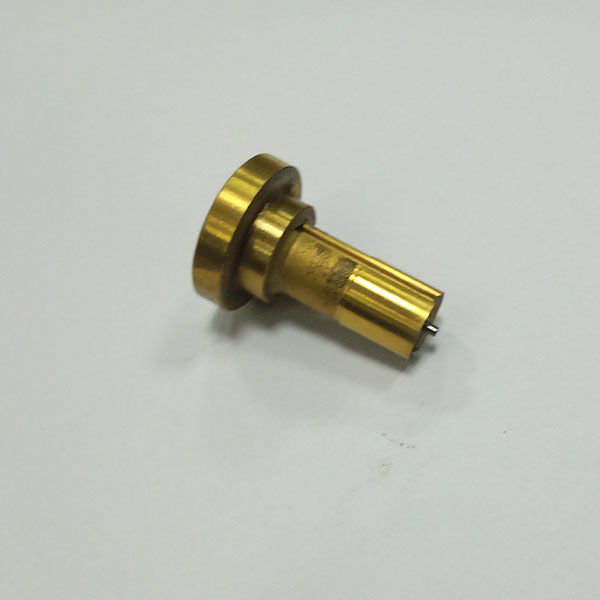
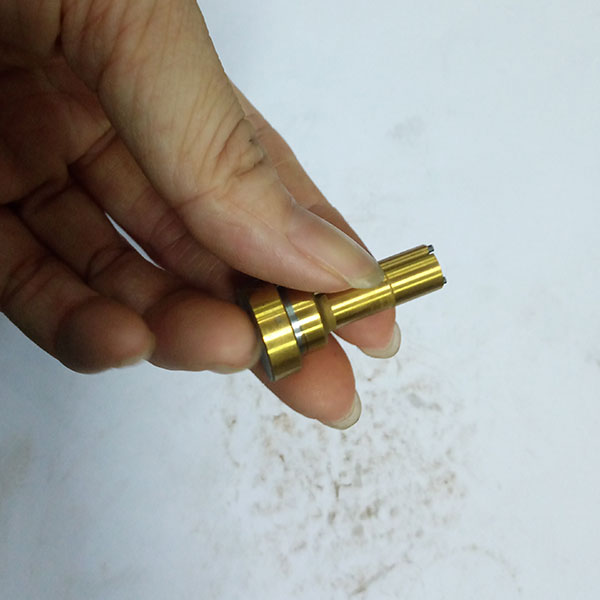
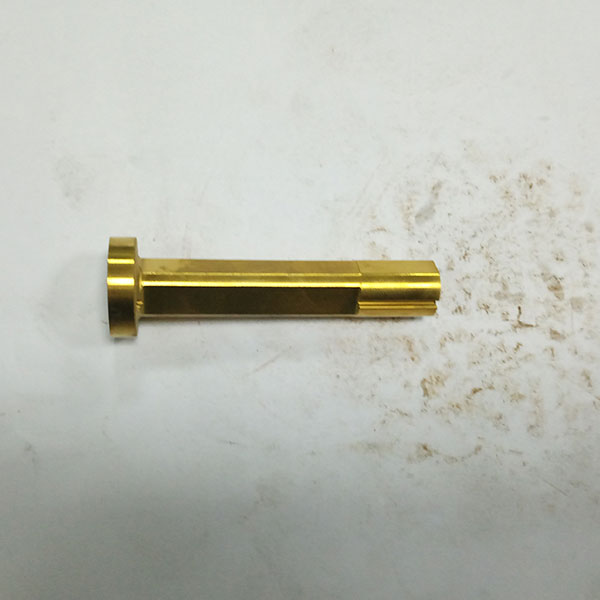
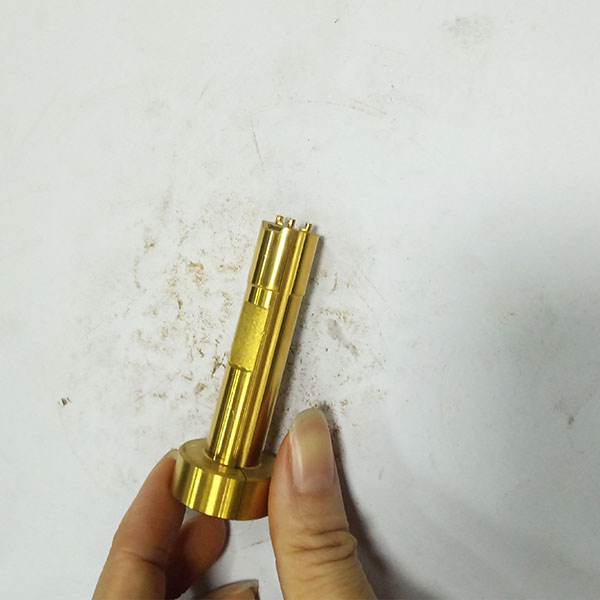
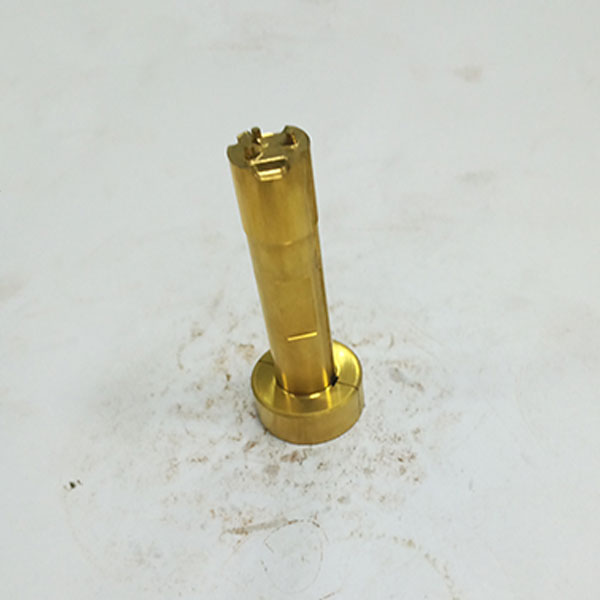
Table of Contents
What Is AlNiCo Magnet(Ferrite Material)
The most original definition of magnetic steel is Al-Ni-Co alloy (AlNiCo is the abbreviation of Al-Ni-Co in English). Magnetic steel is composed of several hard and strong metals, such as iron and aluminum, nickel, and cobalt. Sometimes It is a synthesis of copper, niobium and tantalum to make super-hard permanent magnet alloys. The composition of the metal is different, the magnetic properties are different, and the uses are also different. They are mainly used in various sensors, meters, electronics, electromechanical, medical, teaching, automotive, aviation, military technology and other fields. Alnico magnet is the oldest type of magnet, and is called a natural magnet. Although it is the oldest, its excellent adaptability to high temperatures makes it still one of the most important magnets. Nickel and cobalt can work normally at high temperatures above 500℃, which is his biggest feature. In addition, the corrosion resistance is stronger than other magnets.
Alnico alloy is an iron alloy. In addition to iron, aluminum (Al), nickel (Ni), cobalt (Co) and a small amount of other components that enhance magnetic properties are added. Al-Ni-Co alloy has high coercivity and is a very suitable material for permanent magnets. Al-Ni-Co alloy is hard and brittle, cannot be cold-worked, and must be made by casting or sintering.
To give an example of an anisotropic cast AlNiCo alloy with intermediate properties, Alnico-6 is composed of 8% Al, 16% Ni, 24% Co, 3% Cu, 1% Ti, and the others are all Fe. Alnico-6 has a maximum magnetic energy product (BHmax) of 3.9 million Gauss-Oersted, a coercivity of 780 oersted, a Curie temperature of 860 °C, and a maximum operating temperature of 525 °C.
In 1931, Japanese material expert Mishima discovered a specific composition of Al-Ni-Co alloy (58% Fe, 30% Ni, 12% Al), which had extremely high coercivity and was two of the best magnetic steels of that period. Times.
The Main Characteristics Of Ferrite Magnets
It is manufactured by powder metallurgy:
- -The chemical combination is-Ba/Sr O6 FeO
- -Harder and brittle
- -Not easy to demagnetize
- -Very good corrosion resistance
- -Low price, abundant sources
- -Good temperature stability
- -The most widely used permanent magnet
Permanent Magnetic Material
It is a material with wide hysteresis loop, high coercivity, high remanence, and can maintain constant magnetic properties once magnetized. Also known as hard magnetic materials. In practice, the permanent magnet material works in the second quadrant demagnetization part of the magnetic hysteresis loop after deep magnetic saturation and magnetization. Commonly used permanent magnet materials are divided into Al-Ni-Co-based permanent magnet alloys, Fe-Cr-Co-based permanent magnet alloys, permanent magnet ferrites, rare earth permanent magnet materials and composite permanent magnet materials.
- Al-Ni-Co-based permanent magnet alloy. With iron, nickel, and aluminum as the main components, it also contains copper, cobalt, titanium and other elements. With high remanence and low temperature coefficient, magnetic stability. There are two types of casting alloys and powder sintered alloys. There were many applications in the 1930s to 1960s, and it is now mostly used in the instrument industry to manufacture magnetoelectric meters, flow meters, micro motors, relays, and so on.
- FeCrCo permanent magnet alloy. With iron, chromium, and cobalt as the main components, it also contains molybdenum and a small amount of titanium and silicon. Its processing performance is good, it can undergo cold thermoplastic deformation, its magnetic properties are similar to that of AlNiCo permanent magnet alloys, and its magnetic properties can be improved through plastic deformation and heat treatment. It is used to manufacture all kinds of small magnetic components with small cross-sections and complex shapes.
- Permanent ferrite. There are mainly barium ferrite and strontium ferrite, which have high resistivity and high coercivity, and can be effectively used in large gap magnetic circuits, and are especially suitable for permanent magnets in small generators and motors. Permanent magnet ferrite does not contain precious metals such as nickel, cobalt, etc. It has a rich source of raw materials, simple process and low cost, and can replace AlNiCo permanent magnets to manufacture magnetic separators, magnetic thrust bearings, speakers, microwave devices, etc. However, its maximum magnetic energy product is low, temperature stability is poor, and the texture is brittle, fragile, and not resistant to shock and vibration. It is not suitable for measuring instruments and magnetic devices with precision requirements.
- Rare earth permanent magnet materials. Mainly rare earth cobalt permanent magnet materials and neodymium iron boron permanent magnet materials. The former is an intermetallic compound formed by the rare earth elements cerium, praseodymium, lanthanum, neodymium, etc. and cobalt. Its magnetic energy product can reach 150 times that of carbon steel, 3 to 5 times that of alnico permanent magnet materials, and 8 to that of permanent ferrite. 10 times, low temperature coefficient, stable magnetism, coercivity up to 800 kA/m. Mainly used in low-speed torque motors, starting motors, sensors, magnetic thrust bearings and other magnetic systems. The neodymium iron boron permanent magnet material is the third-generation rare earth permanent magnet material. Its remanence, coercivity and maximum magnetic energy product are higher than the former, not fragile, good mechanical properties, and low alloy density, which is conducive to the light weight of magnetic components. Sizing, thinning, miniaturization and ultra-miniaturization. But its high magnetic temperature coefficient limits its application.
- Composite permanent magnet material is compounded by permanent magnetic substance powder and plastic substance as a binder. Because it contains a certain proportion of binder, its magnetic properties are significantly lower than the corresponding magnetic material without binder. Except for metal composite permanent magnetic materials, other composite permanent magnetic materials are limited by the heat resistance of the binder, so the service temperature is relatively low, generally not exceeding 150°C. However, the composite permanent magnet material has high dimensional accuracy, good mechanical properties, and good uniformity of the performance of each part of the magnet, and it is easy to carry out the radial orientation and multi-pole magnetization of the magnet. Mainly used in the manufacture of instruments and meters, communication equipment, rotating machinery, magnetic therapy equipment and sporting goods, etc.
Classification
The first category is: alloy permanent magnet materials, including rare earth permanent magnet materials (neodymium iron boron Nd2Fe14B), samarium cobalt (SmCo), aluminum nickel cobalt (AlNiCo)
The second category is: Ferrite permanent magnet materials (Ferrite)
According to the different production processes, it is divided into: sintered ferrite, bonded ferrite, and injection molded ferrite. These three processes are divided into isotropic and anisotropic magnets according to the different orientation of the magnetic crystal.
These are the main permanent magnet materials currently on the market, and some are eliminated due to production process or cost reasons, which cannot be used in a wide range, such as Cu-Ni-Fe (copper nickel iron), Fe-Co-Mo (iron, cobalt, molybdenum) ), Fe-Co-V (iron cobalt vanadium), MnBi (manganese bismuth)
1. Rare earth permanent magnet materials (NdFeB Nd2Fe14B)
According to different production processes, it is divided into the following three types:
- Sintered NdFeB-Sintered NdFeB permanent magnets are smelted after jet milling and powder, with high coercivity and extremely high magnetic properties. Its maximum magnetic energy product ( BHmax) is more than 10 times higher than ferrite. Its own mechanical properties are also quite good, and it can cut and process different shapes and drill holes. The maximum operating temperature of high-performance products can reach 200 degrees Celsius. Because of its material content, it is easy to cause rust, so the surface must be treated with different coatings according to different requirements. (Such as zinc plating, nickel, environmental zinc, environmental nickel, nickel copper nickel, environmental nickel copper nickel, etc.). Very hard and brittle, with high resistance to demagnetization, high cost/performance ratio, not suitable for high working temperature (>200℃).
- Bonded NdFeB-Bonded NdFeB is to uniformly mix NdFeB powder with a binder such as resin, plastic or low melting point metal, and then use compression, extrusion or injection molding Compound type neodymium iron boron permanent magnet made by other methods. The product is formed once, without secondary processing, and can be directly made into various complicated shapes. Bonded NdFeB has magnetism in all directions and can be processed into NdFeB compression molds and injection molds. High precision, excellent magnetic properties, good corrosion resistance and good temperature stability.
- Injection molded neodymium iron boron (Zhusu NdFeB)-with extremely high precision, it is easy to make thin-walled rings or thin magnets with complex anisotropic shapes
2. Sintered ferrite
The main raw materials of Sintered Ferrite include BaFe12O19 and SrFe12O19, which are divided into isotropic and anisotropic magnets according to the orientation of the magnetic crystals. Because of its low price and moderate magnetic properties, it has become a widely used magnet at present. Ferrite magnets are manufactured by ceramic technology, and the texture is relatively hard, and it is also a brittle material. Because of its good temperature resistance and low price, ferrite magnets have become more widely used permanent magnets.
3. Rubber magnet
Rubber Magnet is one of the ferrite magnetic material series. It is made of bonded ferrite powder and synthetic rubber through extrusion molding, calendering molding, injection molding and other processes. It is flexible, elastic and twistable.的magnets. It can be processed into strips, rolls, flakes and various complex shapes. Rubber magnets are made of magnetic powder (SrO6Fe2O3), polyethylene (CPE) and other additives (EBSO, DOP), etc., and are manufactured by extrusion and calendering. The rubber magnetic material can be of the same sex or of the opposite sex. It is made of ferrite magnetic powder, CPE and some trace elements. It can be bent, twisted, and rolled. It can be used without more mechanical processing, and the shape can be trimmed according to the required size. The rubber magnet can also be compounded with PVC, back glue, UV oil, etc. according to customer requirements. Its magnetic energy product is between 0.60 and 1.50 MGOe. Application areas of rubber magnetic materials: refrigerators, information signage racks, fasteners for fixing objects to metal bodies for advertisements, etc., magnetic sheets for toys, teaching instruments, switches and sensors. Mainly used in micro-motors, refrigerators, disinfection cabinets, kitchen cabinets, toys, stationery, advertising and other industries.
4. AlNiCo
AlNiCo is the first permanent magnet material developed. It is an alloy composed of aluminum, nickel, cobalt, iron and other trace metal elements. According to different production processes, it is divided into sintered aluminum nickel cobalt (Sintered AlNiCo) and cast aluminum nickel cobalt (Cast AlNiCo). The product shapes are mostly round and square. The casting process can be processed into different sizes and shapes; compared with the casting process, the sintered product is limited to small sizes, and the produced blank has better dimensional tolerances than the cast product blank, and the magnetic properties are slightly lower than the cast product, but it can The workability is better. Among the permanent magnet materials, cast AlNiCo permanent magnets have the lowest reversible temperature coefficient, and the working temperature can be as high as 600 degrees Celsius. Alnico permanent magnet products are widely used in various instruments and other applications.
5. Samarium Cobalt
SmCo is divided into SmCo5 and Sm2Co17 according to the composition, which are the first and second generation rare earth permanent magnet materials, respectively. Because its raw materials are very scarce and expensive, its development is restricted. Samarium cobalt (SmCo), as the second-generation rare earth permanent magnet, not only has a high magnetic energy product (14-28MGOe) and reliable coercivity, but also shows good temperature characteristics in the rare earth permanent magnet series. Compared with NdFeB, samarium cobalt is more suitable for working in high temperature environment (>200℃).
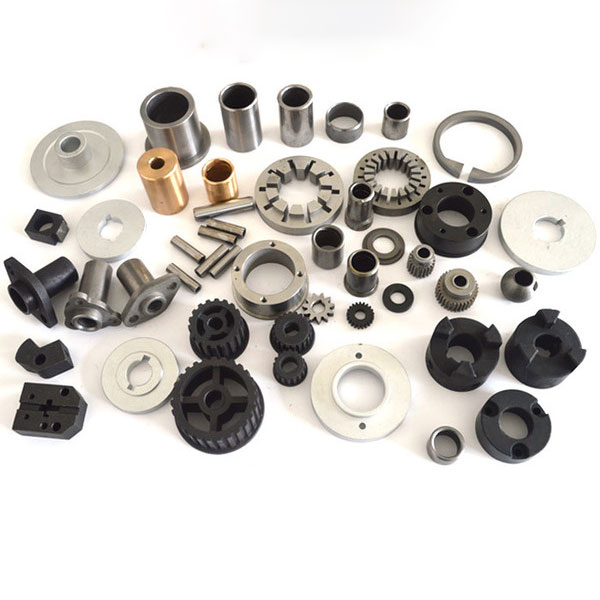