Iron Powder Core Dies | Iron Powder Core Mold
Iron powder core is a relatively common soft magnetic material, and it is also one of the materials with relatively low market prices. This material is composed of carbon-based ferromagnetic powder and resin carbon-based ferromagnetic powder. Due to its low price, the iron powder core is still the most used magnetic powder core, with a permeability between 10 and 100. Iron powder core is a popular term for the magnetic material ferroferric oxide, which is mainly used in electrical circuits to solve electromagnetic compatibility (EMC) problems. In actual application, various other substances will be added according to different filtering requirements under different bands.
When a certain band of clutter passes through the magnetic ring, the electromagnetic characteristics of the magnetic ring cause the current of this band to be converted into magnetic force and part of the heat is consumed.The material of the magnetic ring is more iron powder core (low price, widely used), and advanced rare earth materials.
In the past over 10 years, PTJ has been focusing on technical researching, production and marketing of Carbide dies. And provide the best Carbide dies and various electronic application solutions for cutomers from world wide. You always can find out a suitable Iron Powder Core Dies case studies for your product in our official website.

Standard Iron Powder Core Dies by PTJ:
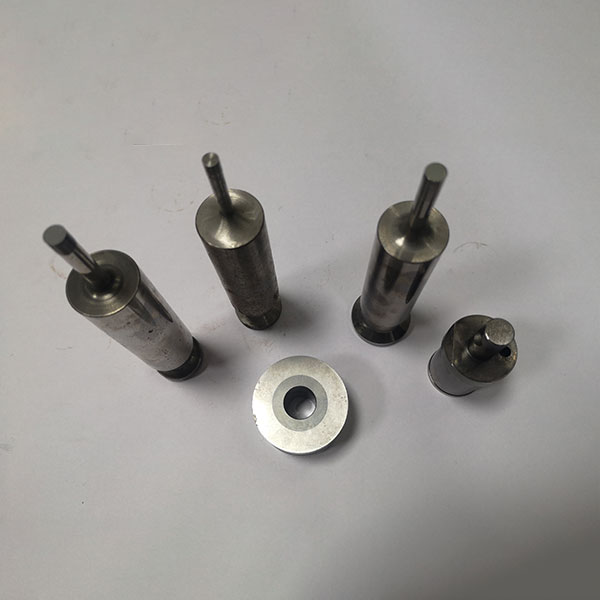
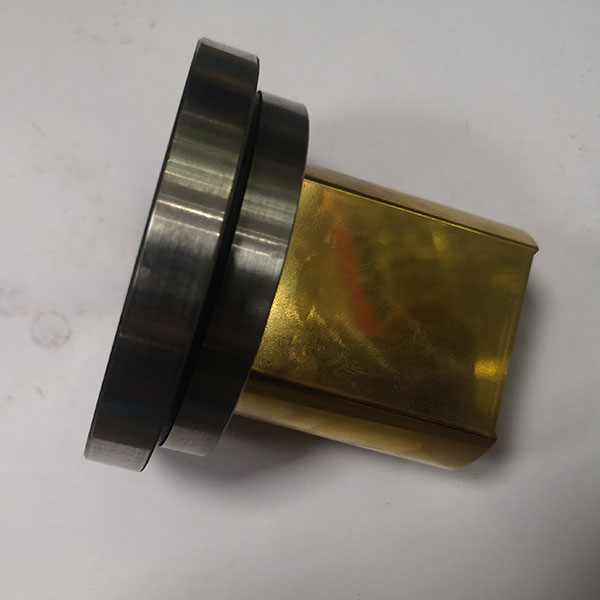
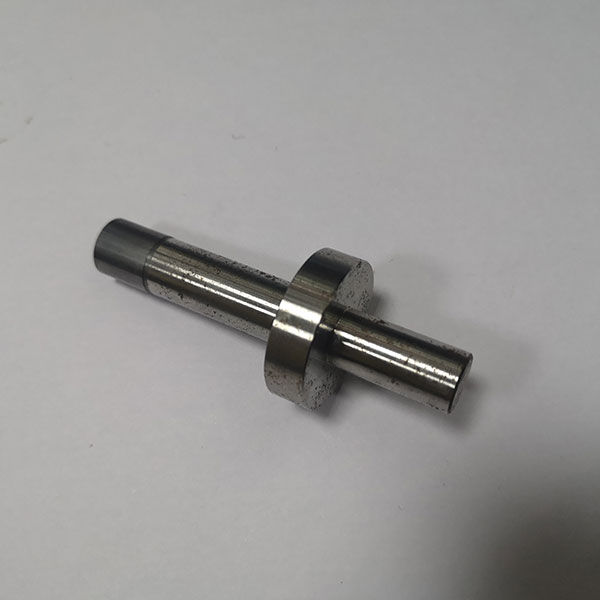
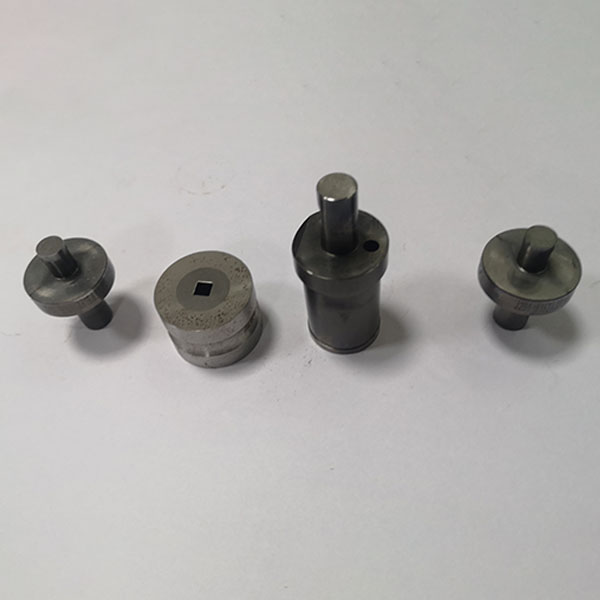
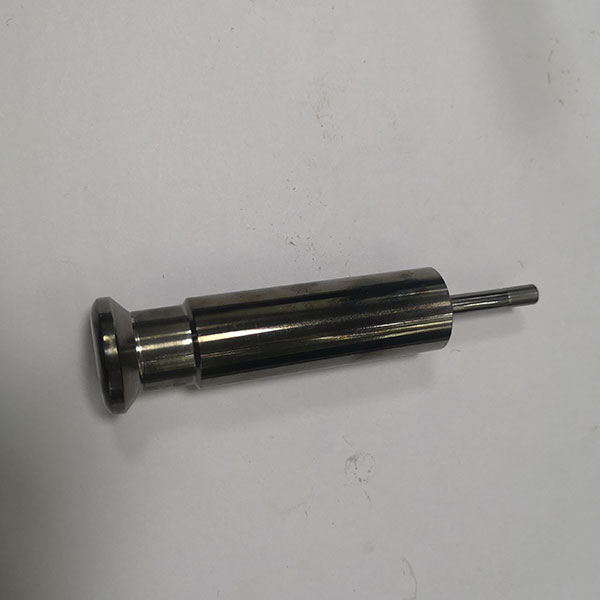
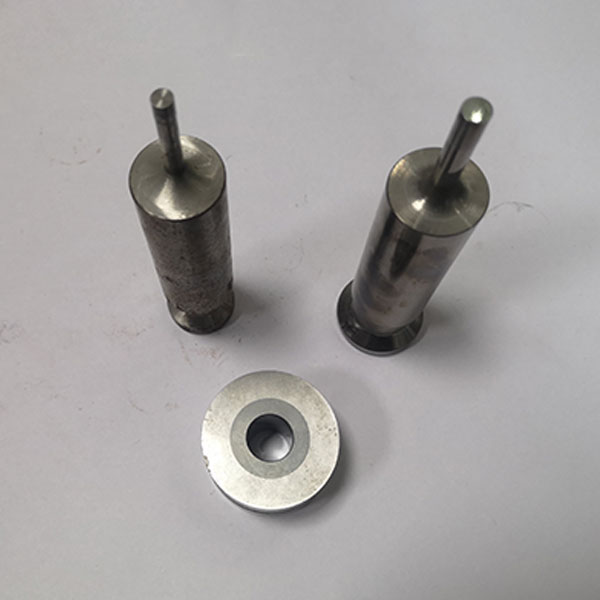
Table of Contents
The Overview Of Iron Powder Core
The Technical Improvement Of Iron Powder Core
Insulation
In the insulation treatment process consisting of mixing and drying, in order to completely insulate the iron powder, the following two points need to be paid attention to:
The first is to select the best surfactant. For the insulation treatment, first add a water-soluble insulation treatment liquid to the iron powder and mix it with a special mixer. At this time, in the insulation treatment liquid, a difference in specific resistance can be found due to the type of surfactant added. Choosing the surfactant with the lowest contact angle can get the highest inherent resistance, which has been fully verified from experiments.
The second is to add an anti-rust agent to the solution. When no anti-rust agent is added, the density and intrinsic resistance value both show the lowest value. When the added amount of rust inhibitor is a certain value, the inherent resistance is the largest and the density becomes larger. The above experimental results show that selecting the best surfactant and adding rust inhibitor are effective for forming a uniform insulating film on the surface of the powder magnetic core.
Temperature
The metal powder used has the same composition as the electrical steel sheet, has good temperature stability, and epoxy resin is also a material with excellent stability. The prepared composite material was tested in the air at 155°C for 1000 hours, and no degradation of the material properties was found.
Noise
Since the magnetic composite material has a large mechanical damping in its structure, the iron core noise is small. When comparing the noise characteristics of a reactor with a ring-shaped ferrite core and a magnetic composite reactor with the same size, shape and inductance, With a sine wave voltage of 500Hz~20KHz, the noise of a reactor made of magnetic composite materials is reduced by about 10db.
For a long time, the magnetic materials used in power electronic devices have been electrical steel materials. In the commercial frequency range, this material has excellent magnetic properties, but as the frequency rises, its properties deteriorate sharply, while ferrite In contrast, the material has excellent high-frequency characteristics, but it cannot be used as a high-power device due to its low saturation magnetic flux density. The powder magnetic core material has excellent high frequency characteristics and high magnetic flux density, and can be widely used in areas where electrical steel and ferrite cannot be used. This material is formed by a mold, can be made into a variety of complex shapes, and has features such as workability. As a new material widely used in the field of power electronics and anti-EMI, attention should be paid.
Sendust Magnetic Powder Core And High-Performance Iron Powder Core
Early magnetic powder cores were "bonded" metal soft magnetic cores made of iron-silicon aluminum alloy magnetic powder. People often refer to this kind of sendust magnetic powder core as "iron powder core". Its typical preparation process is as follows: use Fe-Si-Al alloy magnetic powder (commercially available composition is Fe:Si:Al=84%:10%:6%) to be flattened by ball milling and coated with an insulating layer by a chemical method. Then add about 15wt% of the binder, mix evenly, press and solidify, and finally heat treatment (stress relief) to make the product. This traditional "iron powder core" product mainly works at 20kHz∼200kHz. Because they have much higher saturation magnetic flux density than ferrites working in the same frequency band, good DC superposition characteristics, magnetostriction coefficient close to zero, no noise during operation, good frequency stability, and high cost performance. It has been widely used in electronic components such as high-frequency electronic transformers. Their disadvantage is that the non-magnetic filler not only produces magnetic dilution, but also makes the magnetic flux path discontinuous, and the local demagnetizing field leads to a decrease in magnetic permeability. Therefore, it is mainly used in workplaces that require high Bm but not very strict magnetic permeability.
The recently developed high-performance iron powder core is different from the traditional sendust magnetic powder core. The raw material used is not alloy magnetic powder but pure iron powder coated with an insulating layer. The amount of binder is very small, so the magnetic flux density is increased. Increased. They work in the low and medium frequency bands below 5kHz, generally several hundred hertz, which is much lower than the working frequency of sendust magnetic powder cores. The target market is to replace silicon steel sheets used in motors with its advantages of low loss, high efficiency and easy three-dimensional design.