What Is Powder Metallurgy Mold
In the powder metallurgy molding process, powder metallurgy molds can be used to form loose metal, ceramic, or other material powders in tungsten steel molds into semi-finished products of predetermined geometry, size, density and strength by pressure, and then pass similar to stamping A semi-finished product blank is obtained during the demolding process of the process, and the semi-finished product needs at least a subsequent sintering process to become a finished product. Powder metallurgy molds are named powder metallurgy molds because they serve powder metallurgy projects, also called powder metal molds.
As a leading China Powder Metallurgy Mold company, Soft magnetic material mold and servo motor magnetic tile mold are the specialty of PTJ Dies. We excel in manufacturing high precision, high life custom carbide dies to meet ISO 9001:2015 certification. Our machine shop and dies manufacturing services include EDM,Wire Cutting,Die Cutting,CNC turning, CNC milling, automatic bar machining, multi-spindle machining and more. .
In the past over 10 years, PTJ has been focusing on technical researching, production and marketing of Carbide dies. And provide the best Carbide dies and various electronic application solutions for cutomers from world wide. You always can find out a suitable powder metallurgy mold case studies for your product in our official website.
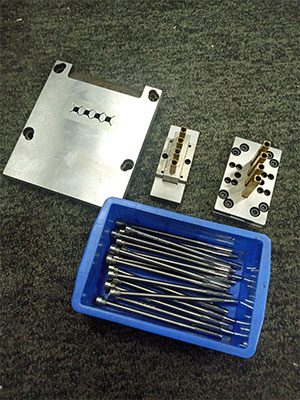
Standard Powder Metallurgy Mold by PTJ:
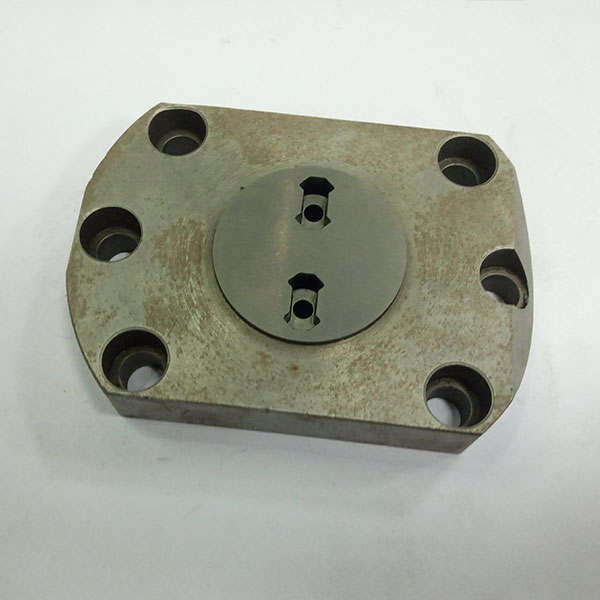
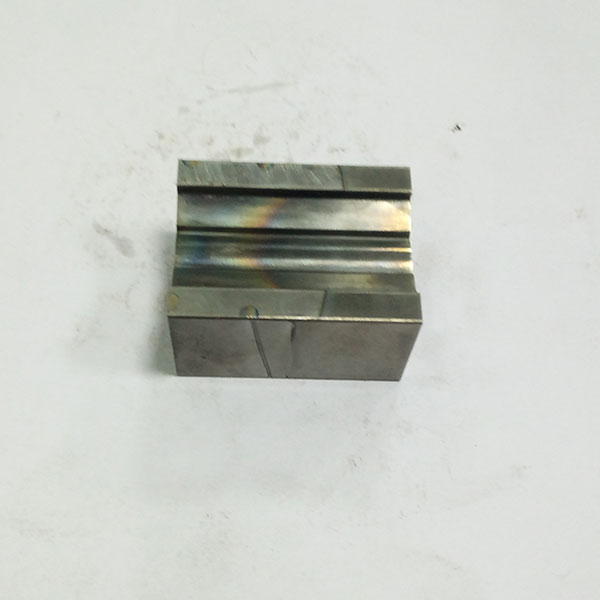
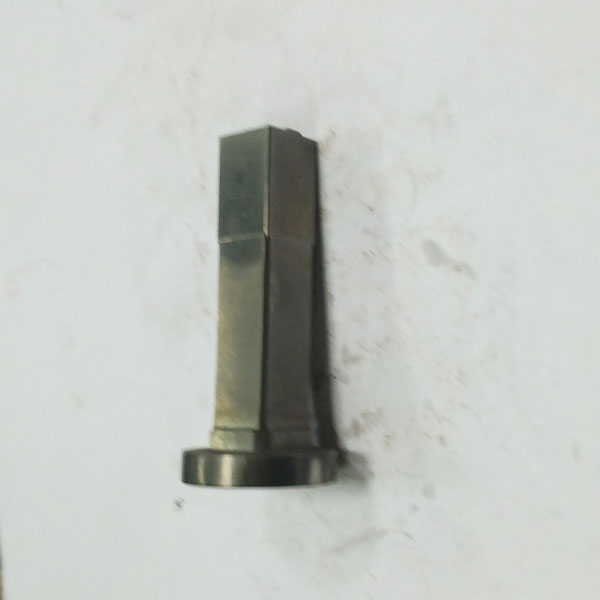
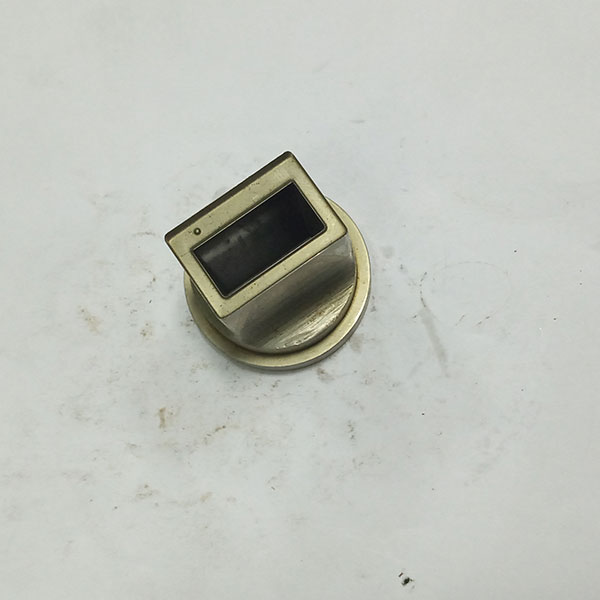
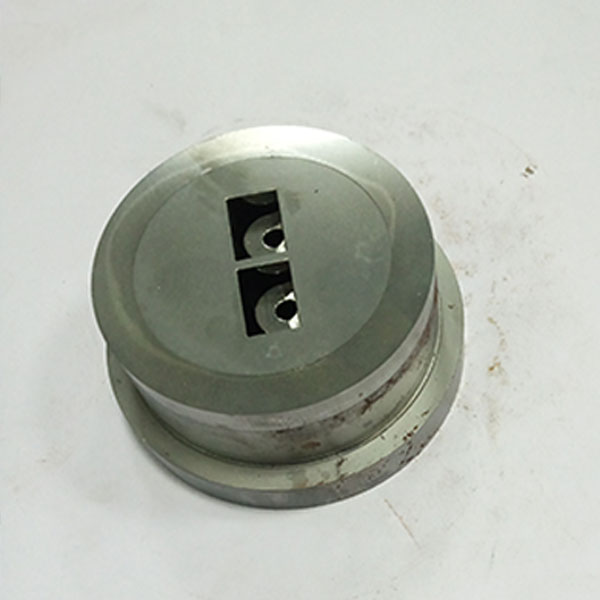
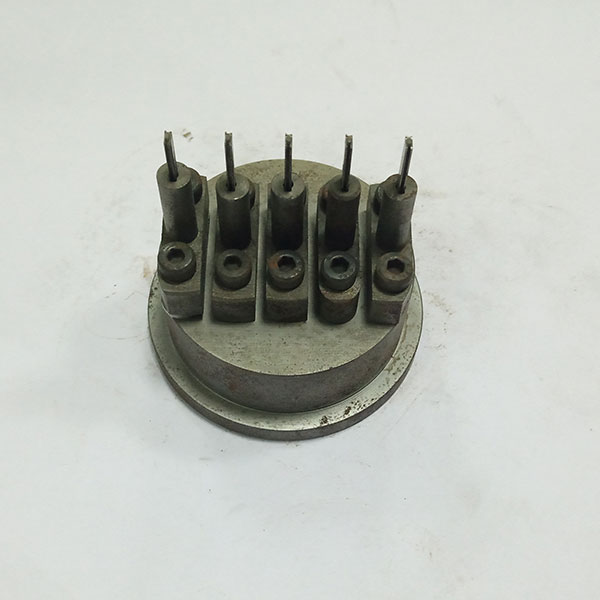
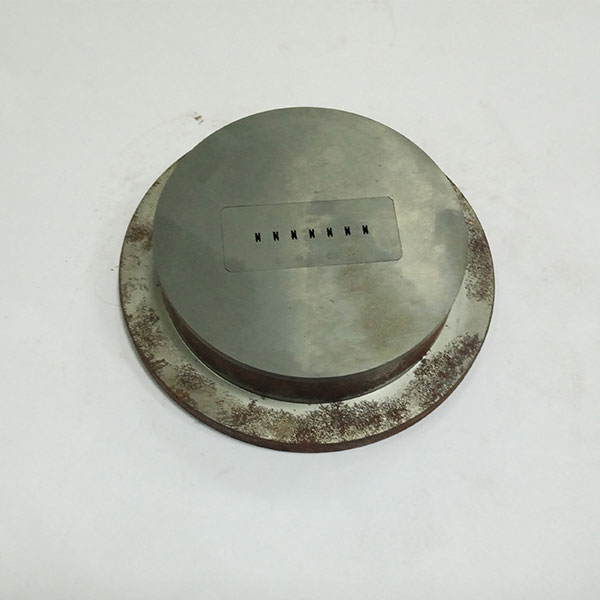
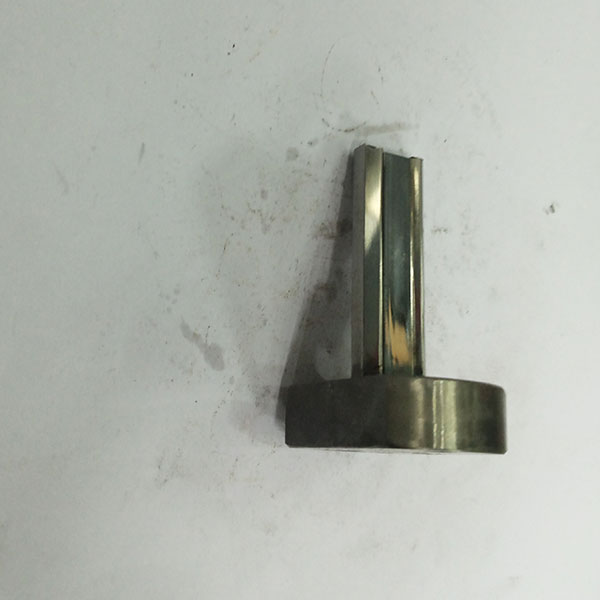
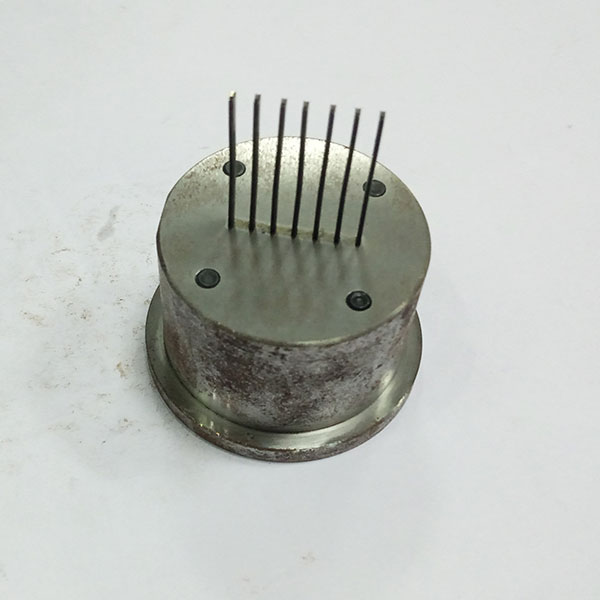
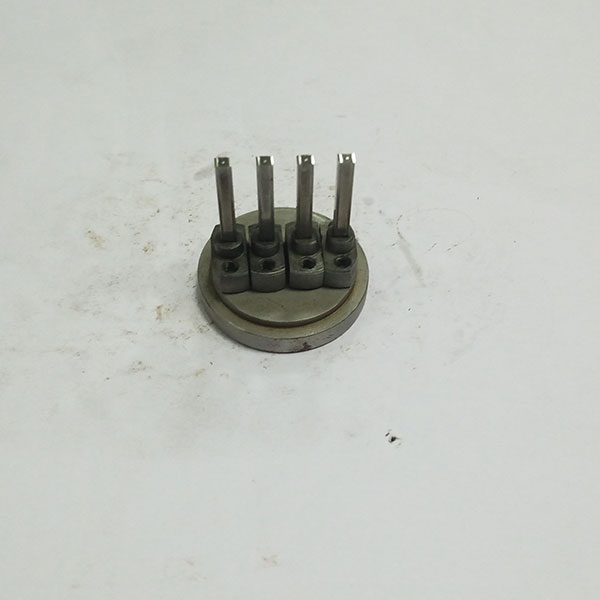
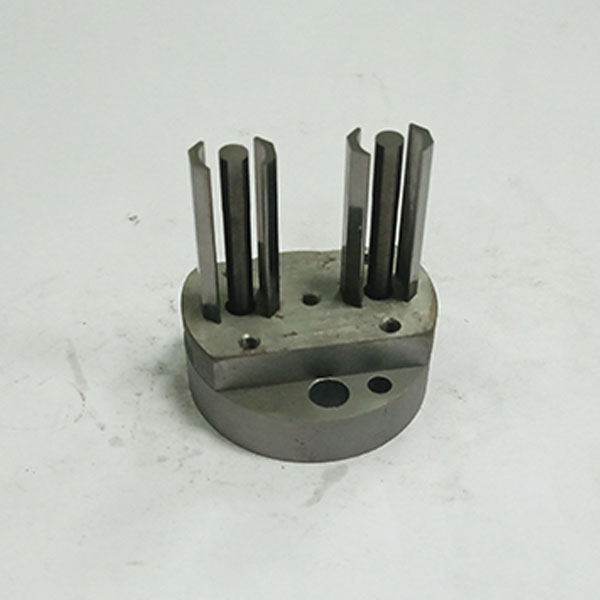
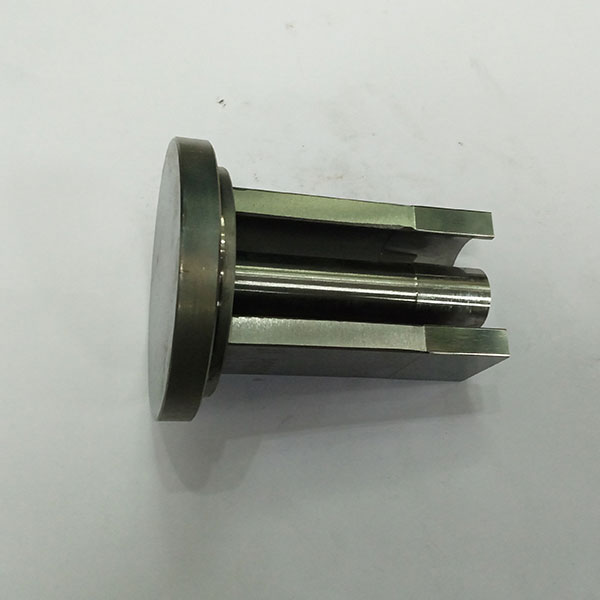
Table of Contents
The Definition Of Powder Metallurgy
Powder metallurgy is an industrial technology for preparing metal powder or using metal powder (or a mixture of metal powder and non-metal powder) as raw materials, forming and sintering, to produce metal materials, composite materials and various types of products. Powder metallurgy technology has been widely used in the fields of transportation, machinery, electronics, aerospace, weapons, biology, new energy, information and nuclear industry, and has become one of the most dynamic branches of new materials science. Powder metallurgy technology has a series of advantages such as significant energy saving, material saving, excellent performance, high product precision and good stability, which is very suitable for mass production. In addition, some materials and complex parts that cannot be prepared by traditional casting methods and mechanical processing methods can also be manufactured by powder metallurgy technology, which has attracted the attention of the industry.
The powder metallurgy products industry in a broad sense includes iron and stone tools, cemented carbide, magnetic materials and powder metallurgy products. The powder metallurgy products industry in the narrow sense only refers to powder metallurgy products, including powder metallurgy parts (accounting for the majority), oil-bearing bearings and metal injection molding products.
The Features Of Powder Metallurgy
Powder metallurgy has unique chemical composition and mechanical and physical properties, and these properties cannot be obtained by traditional melting and casting methods. The use of powder metallurgy technology can directly produce porous, semi-dense or fully dense materials and products, such as oil-bearing bearings, gears, cams, guide rods, cutting tools, etc., which is a rare cutting process.
- Powder metallurgy technology can minimize the segregation of alloy components and eliminate coarse and uneven casting structures. In the preparation of high-performance rare earth permanent magnet materials, rare earth hydrogen storage materials, rare earth luminescent materials, rare earth catalysts, high temperature superconducting materials, new metal materials (such as Al-Li alloys, heat-resistant Al alloys, super alloys, powder corrosion-resistant stainless steel, powder High-speed steel, intermetallic compounds, high-temperature structural materials, etc.) play an important role.
- A series of high-performance non-equilibrium materials such as amorphous, microcrystalline, quasicrystalline, nanocrystalline and supersaturated solid solution can be prepared. These materials have excellent electrical, magnetic, optical and mechanical properties.
- It can easily achieve multiple types of composites, and give full play to the respective characteristics of each component material. It is a process technology for low-cost production of high-performance metal matrix and ceramic composite materials.
- It can produce materials and products with special structures and properties that cannot be produced by ordinary smelting methods, such as new porous biological materials, porous separation membrane materials, high-performance structural ceramic abrasive tools and functional ceramic materials.
- Near-net formation and automated mass production can be realized, thereby effectively reducing the resource and energy consumption of production.
- It can make full use of ore, tailings, steelmaking sludge, rolling steel scale, and recycling scrap metals as raw materials. It is a new technology that can effectively regenerate and comprehensively utilize materials.
Many of our common machining tools and metal abrasives are manufactured by powder metallurgy technology.
The Application Field Of Powder Metallurgy
Powder metallurgy-related companies are mainly suitable for the production and research of parts and accessories in the automotive industry, equipment manufacturing, metal industry, aerospace, military industry, instrumentation, hardware tools, electronic appliances and other fields, production of related raw materials, auxiliary materials, and various powders Manufacturing equipment and sintering equipment. Products include bearings, gears, carbide tools, molds, friction products and so on. In military industrial enterprises, heavy weapons and equipment such as armor-piercing bombs, torpedoes, etc., and brake pairs such as aircraft and tanks need to be produced by powder metallurgy technology. Powder metallurgy auto parts have become the largest market in China's powder metallurgy industry in recent years, and about 50% of auto parts are powder metallurgy parts.
- Application: (automobiles, motorcycles, textile machinery, industrial sewing machines, power tools, hardware tools, electrical appliances, engineering machinery, etc.) various powder metallurgy (iron-copper-based) parts.
- Classification: powder metallurgy porous materials, powder metallurgy antifriction materials, powder metallurgy friction materials, powder metallurgy structural parts, powder metallurgy tool and die materials, and powder metallurgy electromagnetic materials and powder metallurgy high temperature materials.
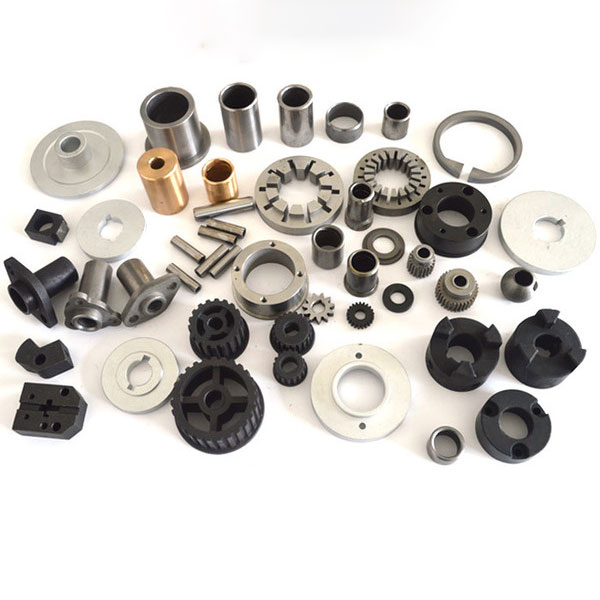
The Preparation Of Powder Metallurgy
- Production of powder. The powder production process includes steps such as powder preparation and powder mixing. In order to improve the moldability and plasticity of the powder, plasticizers such as engine oil, rubber or paraffin are usually added.
- Press molding. The powder is pressed into the required shape under the pressure of 15-600MPa.
- Sintering. It is carried out in a high-temperature furnace or vacuum furnace with a protective atmosphere. Sintering is different from metal melting, at least one element is still in the solid state during sintering. During the sintering process, powder particles undergo a series of physical and chemical processes such as diffusion, recrystallization, fusion welding, compounding, and dissolution, and become metallurgical products with a certain degree of porosity.
- Post-processing. In general, the sintered parts can be used directly. But for some parts that require high precision, high hardness and wear resistance, post-sintering treatment is required. Post-processing includes precision pressing, rolling, extrusion, quenching, surface quenching, oil immersion, and infiltration, etc.
The Preparation Method Of Powder
Making powder is the first step in powder metallurgy. Powder metallurgy materials and products continue to increase, their quality continues to improve, and more and more types of powder are required. For example, from the perspective of material range, not only metal powder, but also alloy powder, metal compound powder, etc. are used; from the perspective of powder shape, various shapes of powder are required. For example, when a filter is produced, it is required to form a powder; from powder In terms of particle size, powders of various particle sizes are required. The coarse powder has a particle size of 500-1000 microns, an ultra-fine powder with a particle size of less than 0.5 microns, and so on. In order to meet the various requirements for powders, there are also various methods for producing powders. These methods are nothing more than turning metals, alloys or metal compounds into a powder state in a solid, liquid or gaseous state. Various methods of preparing powders and powders prepared by various methods. The methods of turning metals and alloys or metal compounds into powders in a solid state include:- There are mechanical pulverization and electrochemical corrosion methods for preparing metal and alloy powders from solid metals and alloys:
- Reduction method for preparing metal and alloy powder from solid metal oxides and salts. Reduction-chemical method for preparing metal compound powder from metal and alloy powder, metal oxide and non-metal powder
- Atomizing method for preparing alloy powders from liquid metals and alloys
- Replacement and reduction of metal salt solutions to prepare metal alloys and coating powders include substitution method and solution hydrogen reduction method; precipitation from molten metal salt to prepare metal powders includes molten salt aging method; from auxiliary metal bath The metal bath method is used to prepare metal compound powder by precipitation.
- There is an aqueous solution electrolysis method for preparing metal and alloy powders from metal salt solution electrolysis; there is a molten salt electrolysis method for preparing metal and metal compound powders from molten metal salt electrolysis.
- Steam condensation method for preparing metal powder from metal vapor condensation;
- Carbon-based thermal dissociation method for preparing metals, alloys and coated powders from gaseous metal carbon-based dissociation
- The vapor-phase hydrogen reduction method is used to prepare metals, alloy powders, and metal and alloy coatings from gaseous metal halide vapor-phase reduction; the chemical vapor deposition method is used to prepare metal compound powders and coatings from gaseous metal halide deposition.
Basic process of powder metallurgy process
- Preparation of raw material powder. The existing milling methods can be roughly divided into two categories: mechanical methods and physical chemical methods. The mechanical method can be divided into: mechanical crushing and atomization method; physical chemical method is further divided into: electrochemical corrosion method, reduction method, chemical method, reduction-chemical method, vapor deposition method, liquid deposition method and electrolysis method. Among them, the most widely used are reduction method, atomization method and electrolysis method.
- The powder is formed into a compact of the required shape. The purpose of forming is to produce a compact of a certain shape and size, and make it have a certain density and strength. The molding method is basically divided into pressure molding and pressureless molding. Compression molding is most widely used in compression molding. In addition, 3D printing technology can also be used for the production of billets.
- Sintering of the compact. Sintering is a key process in the powder metallurgy process. The molded compact is sintered to obtain the required final physical and mechanical properties. Sintering is divided into unit system sintering and multiple system sintering. For solid-phase sintering of unit and multi-component systems, the sintering temperature is lower than the melting point of the metals and alloys used; for liquid-phase sintering of multi-component systems, the sintering temperature is generally lower than the melting point of the refractory components and higher than that of the fusible components. Melting point. In addition to ordinary sintering, there are also special sintering processes such as loose sintering, immersion method, and hot pressing method.
- The subsequent processing of the product. The treatment after sintering can adopt various methods according to different product requirements. Such as finishing, oil immersion, machining, heat treatment and electroplating. In addition, in recent years, some new processes such as rolling and forging have also been applied to the processing of powder metallurgy materials after sintering, and have achieved ideal results.
The Property Of Powder
The general term for all the properties of the powder. It includes: the geometric properties of the powder (particle size, specific surface, pore size and shape, etc.); the chemical properties of the powder (chemical composition, purity, oxygen content and acid insoluble matter, etc.); the mechanical properties of the powder (loose density, fluidity, etc.) , Formability, compressibility, stacking angle and shear angle, etc.); the physical properties and surface characteristics of the powder (true density, gloss, wave absorption, surface activity, ze%26mdash;ta(%26ccedil;) potential and magnetism, etc. ). Powder properties often determine the properties of powder metallurgy products to a large extent. The most basic geometric properties are the particle size and shape of the powder.- Granularity. It affects the powder processing, shrinkage during sintering and the final properties of the product. The performance of some powder metallurgy products is almost directly related to the particle size. For example, the filtration accuracy of the filter material can be obtained empirically by dividing the average particle size of the original powder particles by 10; The big problem is that to obtain finer grain size cemented carbide, it is only possible to use finer grain size wc raw materials. The powder used in production practice has a particle size ranging from a few hundred nanometers to a few hundred micrometers. The smaller the particle size, the greater the activity, and the easier it is for the surface to oxidize and absorb water. When it is as small as a few hundred nanometers, the storage and transportation of the powder is not easy, and when it is too small to a certain extent, the quantum effect starts to work, and its physical properties will change greatly. For example, ferromagnetic powder will become superparamagnetic. Powder, the melting point also decreases as the particle size decreases.
- The particle shape of the powder. It depends on the powdering method, such as the powder obtained by the electrolysis method, the particles are dendritic; the iron powder particles obtained by the reduction method are sponge flakes; the gas atomization method is basically spherical powder. In addition, some powders are egg-shaped, disc-shaped, needle-shaped, onion-shaped, etc. The shape of the powder particles will affect the fluidity and bulk density of the powder. Due to the mechanical engagement between particles, the compact strength of irregular powder is also high, especially dendritic powder has the highest compact strength. But for porous materials, it is best to use spherical powder.
Mechanical Properties
The mechanical properties of the powder are the technological properties of the powder, and it is an important process parameter in the powder metallurgy forming process. The bulk density of the powder is the basis for weighing by volumetric method during compression; the fluidity of the powder determines the filling speed of the powder to the die and the production capacity of the press; the compressibility of the powder determines the difficulty of the pressing process and the pressure High and low; and the formability of the powder determines the strength of the blank. The chemical performance mainly depends on the chemical purity of the raw materials and the method of making powder. Higher oxygen content will reduce compaction performance, green compact strength and mechanical properties of sintered products, so there are certain regulations in most technical conditions of powder metallurgy. For example, the allowable oxygen content of the powder is 0.2% to 1.5%, which is equivalent to an oxide content of 1% to 10%.Powder Pressing
Powder pressing is a powder forming method using external pressure in a press mold. Also known as powder compression molding. The pressing process consists of powder loading, pressing and demolding. The content of powder compaction includes four aspects: powder compaction theory, powder compact, powder compaction mold and powder compaction press.
Suppression Method
During the press forming process, the internal and external friction between the particles and between the particles and the mold wall causes pressure loss to cause uneven forces on each part of the compact, so the density distribution of the compact is uneven. The degree of unevenness is related to the selected suppression method. There are five basic pressing methods: one-way pressing, two-way pressing, floating pressing, pull-down pressing and friction mandrel pressing.
- One-way suppression. The female mold and the core rod do not move, and the upper mold presses unidirectionally. At this time, the external friction makes the density of the upper end of the green compact higher than that of the lower end, and the smaller the diameter of the green compact, the greater the height, and the greater the density difference. Therefore, unidirectional pressing is generally suitable for products with a height-to-diameter ratio H/D≤1 or a set of parts with a height-to-wall thickness ratio H/T≤3.
- Two-way suppression. The female mold is fixed and the upper and lower molds are pressed from both ends at the same time, which is also called simultaneous two-way pressing. If one-way pressure is applied first, and then a reverse one-way pressure is performed at the lower end of the density, it is called non-simultaneous two-way pressure, also known as post pressure. In this way, two-way pressing can be achieved on a one-way pressurizing press. In two-way pressing, if the pressures in the two directions are equal, the low-density layer is located in the middle of the compact; otherwise, the low-density layer moves to the low-pressure end. The density distribution of bidirectional compaction is more uniform than that of unidirectional compaction, and the density difference is reduced. It is suitable for parts with H/D≥2 or H/T≤6.
- Floating suppression. The lower die punch is fixed and the female die is supported by springs, cylinders or oil cylinders and can float up and down. When pressing, the upper die is pressed and the friction between the wall of the female die and the powder gradually increases as the powder is compressed. When the frictional force is greater than the supporting force (floating force) of the spring, etc., the female die and the upper die will descend together, which is equivalent to the upward and reverse compression of the lower die, which acts as a bidirectional compression. In addition to the floating of the female mold during floating pressing, the core rod can also float, and the density distribution at this time is the same as that of the two-way pressing. If the female mold is floating and the core rod does not move, the compact near the female mold is approximately bidirectionally pressed, with the lowest density in the middle; the compact near the core rod is similar to the one-way pressing of the upper die with the lowest density at the lowest end. Floating suppression is suitable for parts with H/T≤6 or H/D≥2.
- Pull-down suppression. Also known as lead-down suppression and forced suppression. At the beginning of pressing, the upper die punch is pressed down for a certain distance, and then descends with the female die (the female die is forced to be pulled down). The lowering speed of the female mold can be adjusted, and the distance it pulls down is equivalent to the distance it floats. When the pressing is finished, the upper die is lifted up, and the female die is further pulled down so that the green compact can be ejected. The density distribution of the compact is similar to that of two-way pressing. Pull-down pressing is suitable for parts with H/T≤6 or H/D≥2. Some powders have low friction and cannot achieve floating compaction. This compaction method can also be used.
- The friction core rod is pressed. During pressing, the female die and the lower die punch are fixed, the upper die punch forces the core rod to move down together, and the speed of the core rod downward movement is greater than the powder downward speed. The friction force between the core rod and the powder can drive the powder down. Thereby, the unevenness of density distribution along the height direction of the green compact can be improved. This method is suitable for pressing H/T>6-10 slender and thin-walled parts.
Influence
The above five basic methods are combined with each other, and there are more pressing methods, which can be used to press compacts with complex shapes. For compacts with varying cross-sections along the pressing direction, such as compacts with steps, slopes or curved surfaces, it is necessary to use combined punching to obtain compacts with uniform density. The newly developed multi-action pressing method and the multi-action floating female die lead-down pressing method are designed with more than two movable upper and lower die punches or core rods, which can be operated separately according to requirements to ensure that each part of the compact The compression ratio is equal, and multi-step parts can be suppressed.
Powder compression molding is the most common molding method, but traditional compression molding also has its limitations. Some non-compressible parts such as radial holes, grooves, internal and external threads, and inverted tapers can only be formed after sintering. However, the newly developed transverse hole forming method and powder moving forming method have eliminated certain limitations and can produce compacts with more complex shapes.