Ceramic Molds | Ceramic Dies Manufacturer
In 1877, the United States used clay as a bonding agent to make abrasive ceramic grinding wheels, which marked the birth of ceramic molds. In 1930, ceramic molds began to select the organization number. In 1970, the ceramic bond cubic boron nitride grinding wheel appeared. In the future, foreign ceramic molds have developed rapidly and have a high level of technology. my country’s ceramic molds have been developed since the 1950s. Ceramic molds have always occupied a major position in the overall composition of abrasive tools. Although with the continuous development of binder materials and the increase of mold types, the output of ceramic molds is in the total mold The output shows a downward trend, but it still occupies a large proportion of the total amount of molds.
- Ceramic molds for structural parts. In some electrical equipment, where wear resistance and insulation are required and the amount is relatively large, structural ceramics will be selected, and the molds for forming such structural parts are called ceramics.
Porcelain structural part mould. - Electronic ceramic molds are mainly product molds for forming ceramic capacitors, varistors, and ceramic heating sheets.
- Most of the craft ceramic molds are wooden molds, which are generally not too complicated in shape and suitable for mass-produced life and decorative ceramic molds.
PTJ has a reputation for successfully machining the ceramic molds other producers prefer not to handle. Customers can confidently design with ceramic, secure in the knowledge that PTJ can machining die even the most exotic, ceramic for a quality, cost effective result.
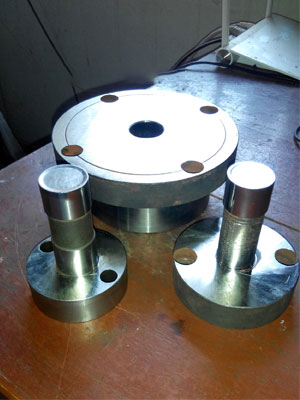
Standard Ceramic Molds by PTJ:
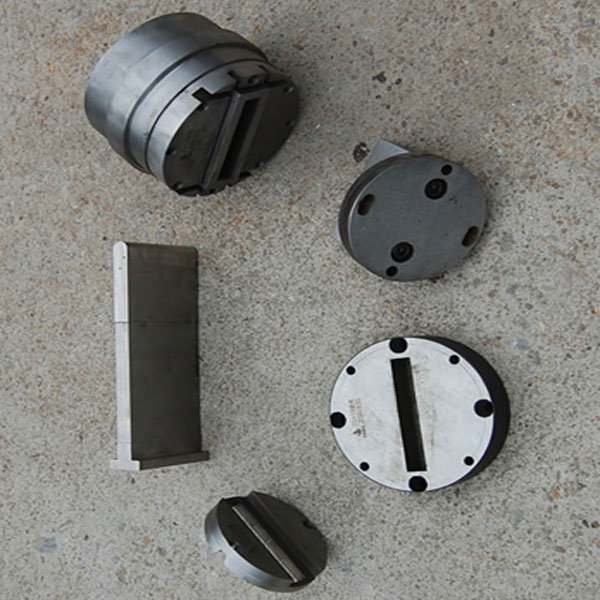
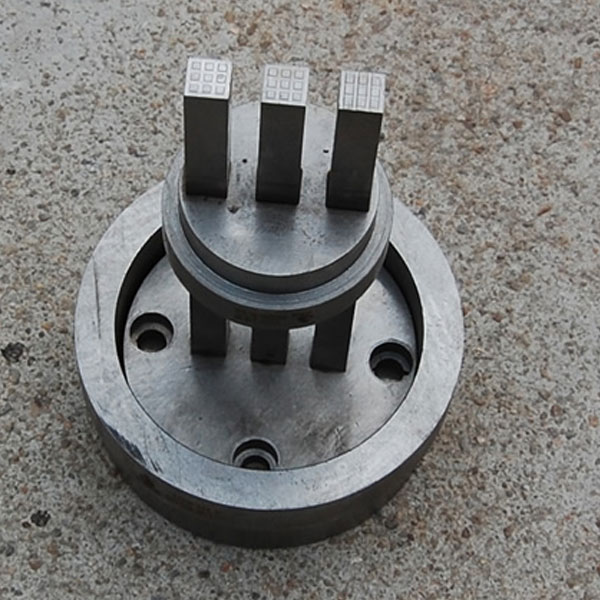
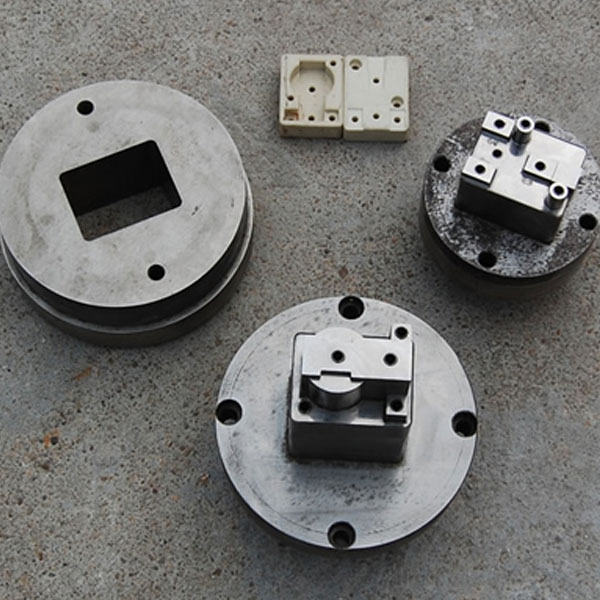
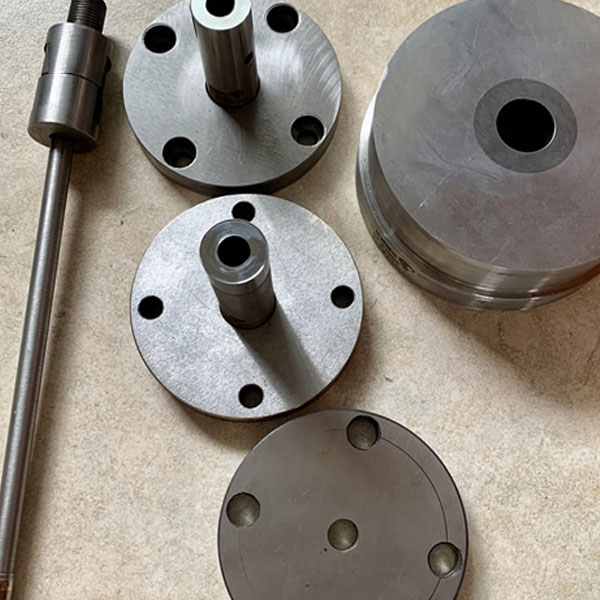
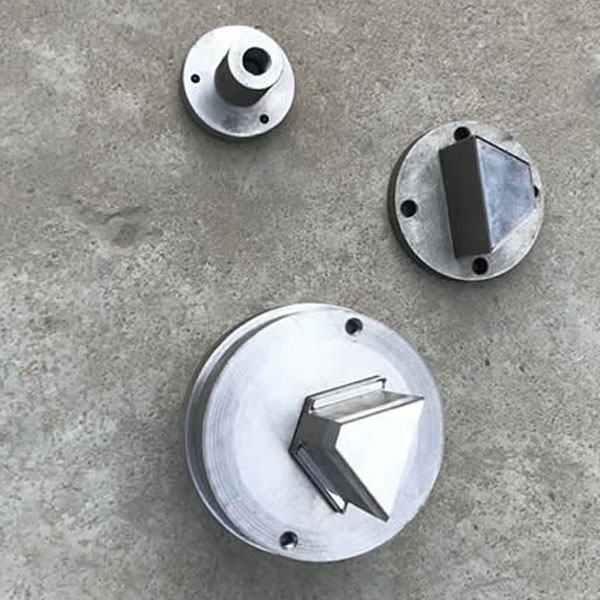
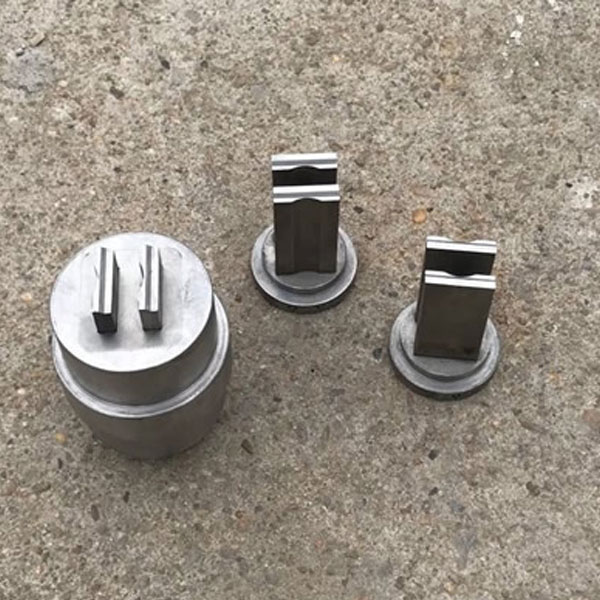
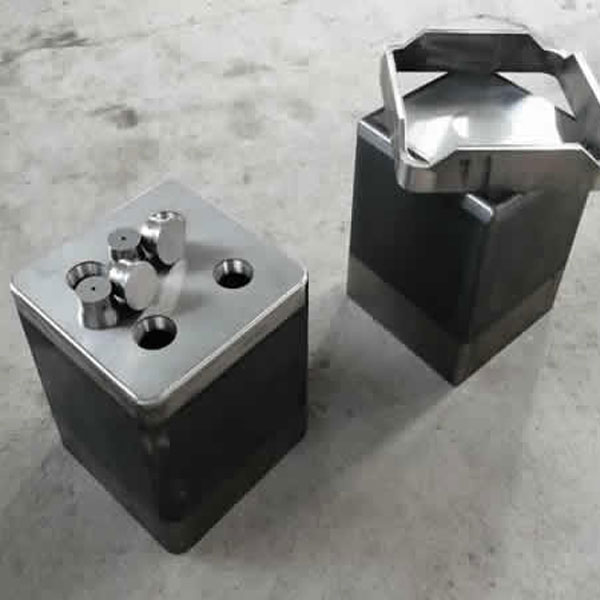
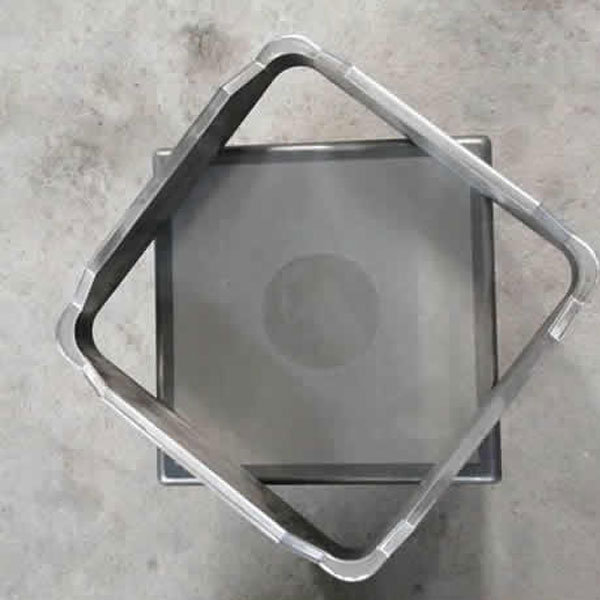
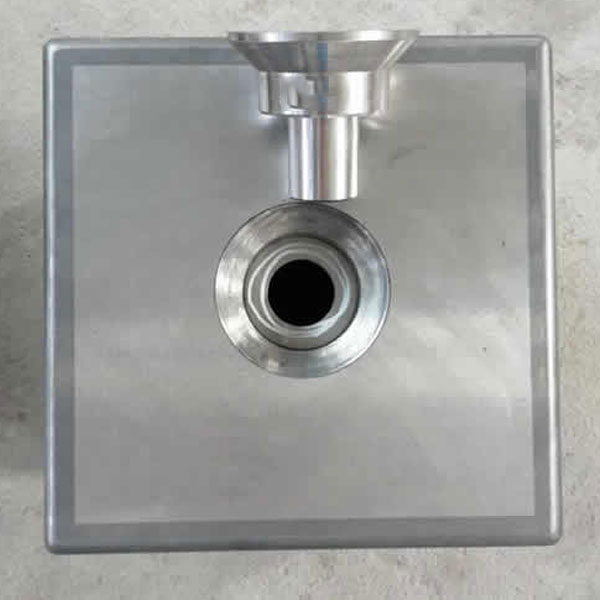
Table of Contents
Ceramic Mold Structure Analysis
Structural Ceramics
Powder molding has a relatively high hardness. The molds are divided into upper molds, lower molds, and concave molds. Some products with holes require mandrels. In order to improve the service life and product consistency, tungsten steel should be used as much as possible for the working parts of the concave mold and the core rod. The upper and lower molds are simple in shape and can also be used for products with large output. If the shape is too complex, especially on the end of the mold Complicated, try to choose mold steel to facilitate processing.
Electronic Ceramics
Powder molding, according to different products, the compaction density will be different, most of the small products are solid small discs, and most of the 20-station rotary presses are used. The mold structure is: upper mold, lower mold, and concave mold; Pay attention to the fit clearance when making, if the clearance is not suitable, it will cause delamination and missing corners.
Large-scale ring-shaped electronic ceramics will be pressed by a nine-station rotary press. The mold structure is: upper mold, lower mold, core rod, and concave mold. When making, pay attention to the contour and matching gap of the mold.
The Application Of Ceramic Molds
Ceramic molds are made of gypsum, which can be divided into high-strength gypsum and ordinary gypsum.
High-strength gypsum is mainly used in machine press production, because the machine press has a certain pressure, so the plaster mold must be able to withstand a certain impact.
Ordinary gypsum is mainly used for grouting and printing blank production, and grouting and printing blanks do not have very high requirements for gypsum.
The Advantages And Disadvantages Of Ceramic Molds
Advantage
High strength, high hardness, moisture resistance, wear resistance, stain resistance, corrosion resistance, high temperature resistance, easy cleaning, small deformation, good insulation, and a certain degree of resistance to rapid cold and heat.
Shortcoming
High brittleness, poor plasticity, poor toughness, and poor thermal conductivity.